In terms of general lighting, LED technology can meet the requirements of producing high-quality lamps, but when it comes to producing high-quality LED lamps, you need to master the three fields of power electronics, optics and thermal management. There are very few engineers who are proficient in three areas at the same time, and if the power engineer is also responsible for the system architecture, he will probably put more effort into controlling the accuracy of the output current. There is no doubt that accuracy is very important, but when our final product is a luminaire, the quality of the light it emits is the focus of our concern. This article focuses on how to strictly control the LED drive current, because when we care about the output light quality, the control of the LED drive current will become an important factor affecting the LED power supply cost. In order to make the most of every penny used in LED power supply design, we propose an optimal solution in this paper—the control loop that closes the actual light output.
The emergence of the emerging field of semiconductor lighting has made engineers who specialize in three areas of power electronics, optics and thermal management (mechanical engineering) a sought-after talent. At present, there are not many engineers with experience in three fields, and this usually means that the background of the system engineer or the overall product engineer is related to these three areas, and they also need to cooperate with engineers in other fields as much as possible. System engineers often bring their habits or accumulated experience in the original field into the design work, which is the same as what an electronic engineer who mainly studies digital systems turns to solve power management problems: they may rely on simplicity. The simulation, not on the test bench to test the power supply, directly on the board, because they did not realize: switching regulators need to carefully check the board layout; in addition, if not tested by the test bench, the actual working situation is very Difficult to match the simulation.
In the process of designing LED luminaires, when the system architecture engineer is a bit electronic power expert, or if the power supply design is contracted to an engineering company, some common habits in standard power supply design will appear in the LED driver design. Some habits are useful because LED drivers are very similar in many ways to traditional constant voltage sources. Both types of circuits operate over a wide range of input voltages and large output power. The other two types of circuits face the challenges of connecting to AC power, DC regulated power rails or batteries. . Power electronics engineers are accustomed to always want to ensure high accuracy of the output voltage or current, which is not a good habit for LED drivers. Digital loads such as FPGAs and DSPs require lower core voltages, which in turn require tighter control to prevent higher bit error rates. Therefore, the tolerances of the digital power rails are usually controlled within ±1% or less than their nominal values, and can also be expressed in absolute values, such as 0.99V to 1.01V. When introducing the design habits of traditional power supplies into the field of LED driver design, the problem is that in order to achieve strict control of the output current tolerance, more power will be wasted and more expensive components will be used, or both. .
Make the best use of every budget
The ideal power supply is not expensive, the efficiency can reach 100%, and it does not take up space. Power electronics engineers are accustomed to listening to customers, and they will do their utmost to meet those requirements in an effort to design the system within the smallest space and budget. In the LED driver design is no exception, in fact it faces greater budget pressure, because the traditional lighting technology has been fully commercialized, and its price has been very low. Therefore, it is very important to spend every penny under the budget. This is also the place where some power electronics designers are being used to 'misleading'. To control the accuracy of the LED current to the same accuracy as the supply voltage of the digital load, it wastes power and wastes money. 100mA to 1A is the current range for most current products, especially the current 350mA (or, more precisely, the current density of the optoelectronic semiconductor junction is 350mA/mm2), which is a compromise between thermal management and lighting efficiency. The integrated circuit that controls the LED driver is germanium-based, so there is a typical bandgap in the 1.25V range. To achieve a 1% tolerance at 1.25V, a voltage range of ±12.5mV is required. This is not difficult to achieve, and a variety of low-cost voltage reference circuits or power control ICs that can achieve such tolerances or better tolerances are inexpensive. When controlling the output voltage, the output voltage can be fed back with a high-precision resistor at very low power (as shown in Figure 1a). In order to control the output current, some adjustments need to be made to the feedback mode, as shown in Figure 1b. This is the only and simplest means of controlling the output current.
After in-depth research, one of the main drawbacks of doing this is that the load and feedback circuits are identical. The reference voltage is applied to a resistor in series with the LED, which means that the higher the reference voltage or LED current, the greater the power consumed by the resistor. Therefore, the reference voltage of the first-generation dedicated LED driver integrated circuit is much lower than the current product, which is similar to the battery charger. Lower voltage means lower power consumption, which means smaller, cheaper, lower loss current sense resistors. In the simple low-end feedback environment shown in Figure 1b, 200mV is a conventional voltage selection. However, to achieve a ±1% tolerance at a 200mV reference voltage, a very expensive integrated circuit is required, with a tolerance of ±2mV relative to the nominal reference voltage. Although this is not impossible, higher accuracy requires higher costs. The ±2mV tolerance requires the production, test, and grading techniques required for high-precision voltage references, where additional costs should be spent on smarter LED drivers. The value of the new cost is the addition of a feedback loop with which the light output (rather than the current output) can be used to control how the LED is driven.
Measuring light output
Just as digital product designers take analog solutions when they encounter uncertainties in power supply design, system architects from power electronics engineers think of high-precision outputs when designing LED luminaires . LED manufacturers have made it clear that the luminous flux is proportional to the forward current. With the same current driving all the LEDs, each LED produces the same luminous flux. Therefore, the power electronics engineer will conclude that high precision current is a must. In this way, they forget that the lumens and lux values ​​of the light output (instead of the amperage) are the focus. Measuring current is easy, and in contrast, measuring light requires expensive large equipment, such as the integrating sphere shown in Figure 2, and most electronics engineers don't know much about the integrating sphere.
3 in 1 Custom Usb Flash Drive Type-C 8G 16G 32G 64G. Easy to transmit data between Micro-USB, USB and Type-C port devices, such as macbook, Type-c smartphone and tablet, Android smartphone and tablet, computuer and laptop. No need any adaptors, sharing data conveniently and save time.
Black Type C Card Reader
This product is suitable for OTG-enabled Type-C interface phone. Easy to copy the memory card data to the phone, such as photos, video clips, office documents, etc. Support microSD, TF card. Can also be used directly to read U disk.
Type C Dual Port Usb Flash Drive TF SD Card Reader
OTG supported. Read TF/SD card directly on your USB C , Micro USB OTG supported devices and other USB port device. Adding an memory card, turns your card reader into a U Flash Disk. Aluminum Shell.Slim,light and fashion design, portable and convenient for using. 3 in 1 : Compatible with USB C device,Micro USB OTG supported devices and USB port device.
OTG Functions Usb Type C 3.1 Flash Drive
Unique 3 in 1 Multifunctional Design: USB 3.1 Type C, USB Type A and Micro USB card reader.
Support OTG, allows you to transfer and share your content between new-generation Smartphones, tablets and laptops with USB Type-C ports.
USB 3.1 Type C Compatible: Connect your TF card with the latest USB-C devices.
Fully compatible with USB 2.0, the reader transfers files quickly and efficiently. Even bulky files like HD video will transfer within minutes.
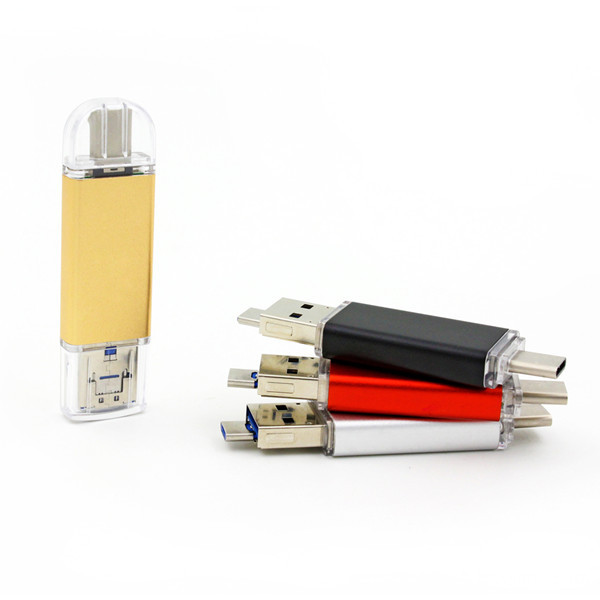
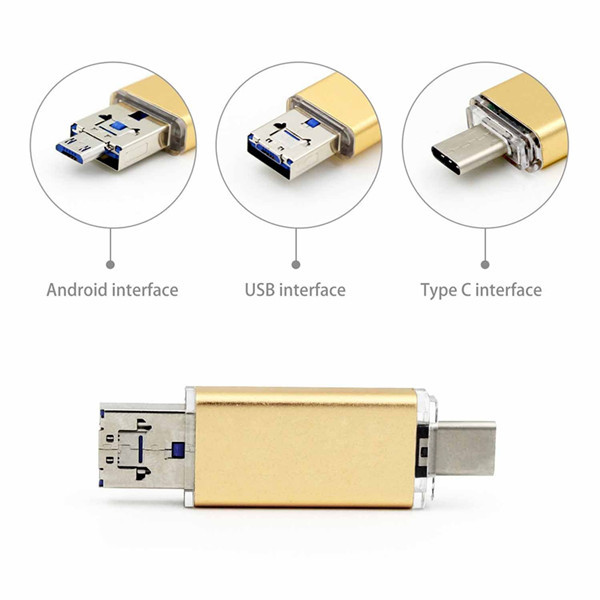
We are a professional Chinese manufacturer of USB Flash Drive , and looking forward to your cooperation!
3 in 1 Dual Port USB Flash Drive, Type C USB Flash Drive, 2017 Usb C Type Flash Drive, 8GB USB Flash Drive For MacBook Type-c Mobile Phone
Reteck Storage Device Co., Ltd. , http://www.reteck.com