Current detection in automotive applications includes controlling the current through the solenoid and injector. For example, in diesel injection, we use 48V or higher voltage to quickly increase the current of the induction injector to 20 amps. Once it reaches 20A, the current detection circuit will provide a feedback signal to the control circuit to keep the injector current at 20A unchanged. Current detection often enhances important performance or characteristics. Power window systems are a good example of the advantages of current detection technology. Since the torque of the motor is proportional to the current, the motor will stop working when the torque is too large. For example, if the human arm is stuck on the power window or the mechanical system fails, the motor will stop working. Current detection method
Current detection can be performed on the low or high voltage side of the load or power supply. The common mode voltage refers to the voltage on the shunt (not the differential voltage on the shunt), which is detected as zero volts on the low voltage side. Low-voltage side detection is the simplest, and the most basic amplifier circuit can be used. The difficulty of low-voltage side detection is that low-voltage side detection will affect the ground of the system, and may need to add more lines, and this method is usually not conducive to fault diagnosis. The high-side shunt amplifier in Figure 1 can detect very low differential voltages (typically 100mV or less) on very high power supply voltages, typically 13.8V in automotive applications. However, if it is an uncondited battery line, it will be affected by transients: if the battery direction is inadvertently misaligned, a condition of –13.5V will occur, and if a load dump or inductive kickback occurs, the maximum transient It can reach 72V. It is conceivable that the amplifier is usually powered by a single power supply of 5-12V (5V power supply is increasingly common), which requires the input pin of the amplifier to be connected to the common mode potential, which greatly exceeds the limit of the amplifier power rail.
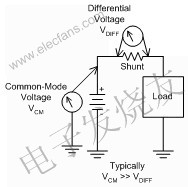
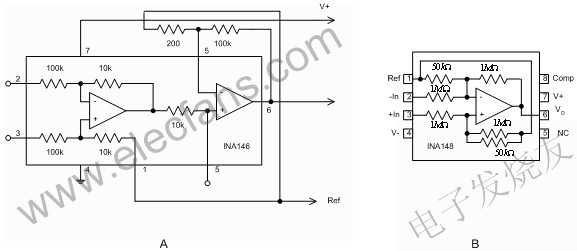
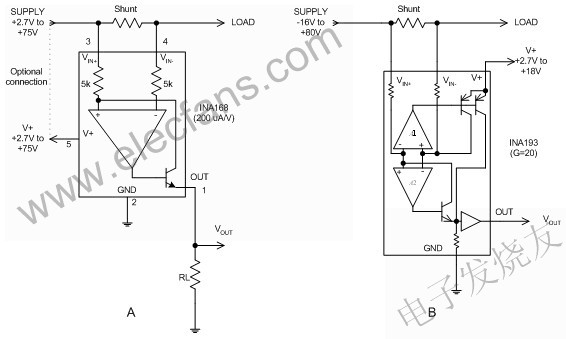
On-board current detection is divided into two major types: one is directly connected to the battery, and the other is connected through a protection circuit that limits transient offset. The above conditions will affect the common mode voltage rating requirements on the current shunt monitor. The maximum voltage of the 12V electronic system in the vehicle is 14.4V, but the transient voltage on the battery bus device can reach up to 75V, and even battery pole switching may occur. We also need to consider another common mode situation: the shunt of the power line is turned on, and the ground is shorted. At this time, the common mode voltage is zero. It must be checked when the current flows, that is to say, the amplifier must also work properly at zero common mode voltage. Finally, let us consider the case of a pulse width modulation (PWM) solenoid driver as shown in Figure 4. In this example, the battery voltage is reached when the top of the solenoid is turned on. When the switch is closed, the voltage will return to the negative level of the diode voltage drop. This requires that the current shunt monitor can still operate at a common mode voltage as low as –2V.
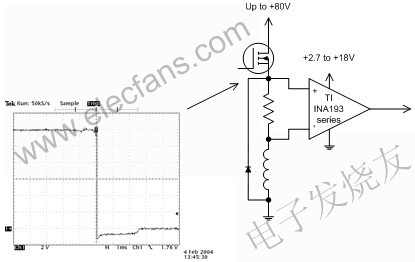
In many applications, the current should be compared with a set value. Generally speaking, current shunt monitor, comparator and reference voltage are also needed for current comparison. In addition, the ideal comparator output should be well compatible with most common logic circuits. Figure 5 shows an example of current comparison. In this example, the current is compared to a simple single-voltage node using TI INA200 series current shunt monitors and comparators. R1 and R2 form a voltage divider to set the voltage node according to the built-in 0.6V voltage node of the INA200 series comparator. (The gain of the INA200 series is very characteristic: the gain of INA200 is 20, the gain of INA201 is 50, and the gain of INA202 is 100.)
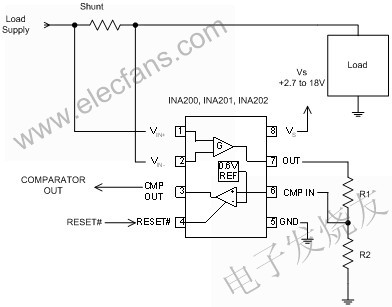
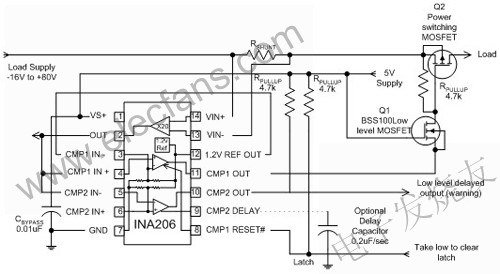
China Electric Water Boiler Urn Suppliers
Here you can find the related products in Electric Water Boiler Urn , we are professional manufacturer of Electric Water Boiler Urn, Hot Water Urn ,Electric Hot Water Dispenser, Large Water Boiler ,Big Water Boiler with Reservoir and Taps,Commercial Electric Water Boiler Urn,We focused on international export product development, production and sales. We have improved quality control processes of Commercial Electric Water Boiler Urn to ensure each export qualified product.
If you want to know more about the products in Commercial Electric Water Boiler
Urn, please click the product details to view parameters, models, pictures,
prices and other information
about Electric Water Boiler Urn,portable hot water dispenser,hot water
dispenser for tea,hot water urn shabbat, tea boiler,Folding Travel Water
Kettle,folded silicon Water Bottle Mini Folding outdoor tea Kettle.
Whatever you are a group or individual, we will do our best to provide you with
accurate and comprehensive message about Commercial Electric Water Boiler Urn!
Commercial Electric Water Boiler Urn
Electric Water Boiler Urn,Hot Water Urn,Electric Hot Water Dispenser,Large Water Boiler,Big Water Boiler with Reservoir and Taps,Commercial Electric Water Boiler Urn
FOSHAN FORTUNE ELECTRICAL APPLIANCE CO.,LTD , https://www.coffelady.com